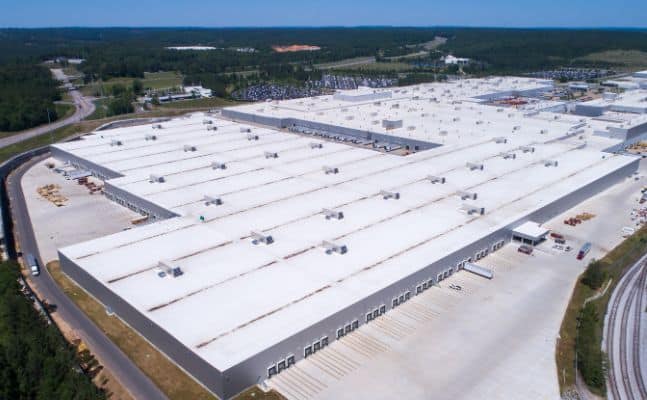
22 Mar Ultimate Checklist to an Industrial Roof Inspection
Regular industrial roof inspections are pivotal in maintaining the efficiency, durability, and longevity of your roofing system. An effective inspection can preempt costly repairs and extend the life of your roof. This blog post unfolds a comprehensive checklist for conducting a meticulous industrial roof inspection, tailored to enhance your facility’s durability without delving into the structural aspects of the building.
The Essence of Industrial Roof Inspections
Industrial roofs withstand a barrage of environmental stressors, from severe weather conditions to mechanical impacts. Proactive inspections are crucial to identifying minor issues before they escalate, ensuring your roof remains in prime condition to support your operational needs.
Preparing for an Industrial Roof Inspection
Review Historical Data: Analyze previous inspection reports and maintenance records. This helps identify patterns or persistent issues that need closer examination.
Timely Scheduling: Optimal timing for inspections is during milder weather conditions to minimize risks and ensure accurate assessments. Aim for bi-annual inspections in the spring and fall to evaluate the roof’s condition post-extreme weather seasons.
Comprehensive Industrial Roof Inspection Checklist
1. Surface Conditions:
Inspect for signs of wear such as cracks, blisters, or splits in the membrane.
Identify any loose, damaged, or missing materials that could compromise roof integrity.
2. Drainage Systems:
Check gutters, downspouts, and internal drainage for blockages that could lead to water pooling.
Look for signs of standing water which might indicate drainage issues.
3. Penetrations and Seals:
Thoroughly examine areas around roof penetrations (vents, skylights, pipes) for proper sealing and flashing.
Assess for any deterioration or gaps in seals that could allow water ingress.
4. Membrane and Coverings:
Evaluate the condition of the roof membrane or coverings for any evidence of deterioration or damage.
Ensure all coverings are securely fastened and free of wear or tears.
5. Roofing Accessories:
Inspect mounted accessories or equipment to ensure they’re securely attached without impairing the roof membrane.
6. Debris and Vegetation:
Remove any debris or vegetation accumulation that can retain moisture or obstruct water flow on the roof.
7. Environmental Wear:
Identify any damage potentially caused by environmental conditions, including UV exposure, wind, or chemical exposures.
Post-Inspection Protocol
- Documentation: Compile a detailed report of the inspection findings, supplemented with photographs and a comprehensive description of identified issues.
- Repair Prioritization: Use the inspection report to prioritize repairs, addressing critical concerns promptly to maintain roof integrity and functionality.
- Professional Consultation: For complex issues or when in doubt, consulting with a roofing professional or an independent roof inspection consultant can provide specialized guidance for addressing your roof’s needs.
Alliance Consulting & Testing: Your Partner in Industrial Roof Inspections
An industrial roof inspection transcends mere maintenance—it is a strategic approach to safeguarding your facility’s roofing system against premature wear and costly disruptions. Following the outlined checklist not only facilitates a meticulous evaluation but also paves the way for informed decision-making regarding roof care.
In navigating the complexities of industrial roof maintenance, the expertise of Alliance Consulting & Testing becomes invaluable. With a commitment to precision and excellence, Alliance stands ready to assist in translating the insights gained from your inspections into actionable strategies. This partnership ensures your roofing system not only meets but exceeds expectations, securing the longevity and integrity of your industrial roof with unmatched professionalism.